Corrugated galvanised iron facts for kids
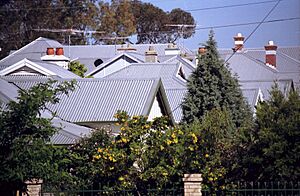
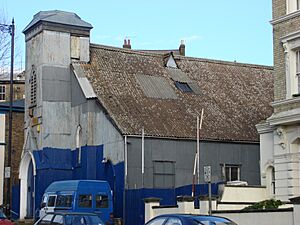
Corrugated galvanised iron (often called CGI or just corrugated iron) is a popular building material. It's made from sheets of steel that have been given a wavy, ridged pattern. This wavy shape makes the sheets much stronger.
Even though it's called "iron," it's actually made of steel. Steel is a strong metal made mostly from iron, with a little bit of carbon added. The "galvanised" part means the steel has a special coating of zinc. This zinc coating helps protect the steel from rust.
Corrugated iron is light and easy to move around. Because of this, it's been used for many buildings, especially in the countryside and for military camps. It was very important in helping countries like Australia grow from the 1840s. It's still used today in many developing countries.
Contents
The Story of Corrugated Iron
The idea for corrugated iron came from Henry Robinson Palmer in 1829. He was an architect and engineer in London. He got a special permission, called a patent, for his "indented or corrugated metallic sheets."
At first, it was made from a type of iron called wrought iron. People quickly found out it was light, strong, and didn't rust easily. It was also simple to transport. This made it perfect for buildings that needed to be put up quickly or by workers who weren't highly skilled.
Soon, corrugated iron became a common building material in many places. This included rural areas in the United States, Argentina, Spain, New Zealand, and Australia. Later, it became popular in India too. In Australia and Argentina, it's still a very common material for roofs, even in cities. In places like Australia and New Zealand, it's become a part of their culture. It's even used in stylish new buildings.
When used for roofs, the sheets are laid like tiles. They overlap a bit on the sides and at the ends to stop water from getting in. Corrugated iron is also widely used for large industrial buildings around the world.
Over time, steel replaced wrought iron for making these sheets, starting around the 1890s. You can't find iron corrugated sheets anymore, but people still call it "corrugated iron." Newer types of metal sheets with different shapes and coatings are also becoming popular, but traditional corrugated iron is still very common.
How Corrugated Iron is Made Today
Today, corrugated iron is made using a process called roll forming. This is a very modern way of making things. It uses machines to do most of the work. This helps to make many sheets quickly and keep costs low.
In this process, flat metal sheets are unrolled from huge spools. They then pass through special rollers called dies. These rollers press the wavy pattern into the metal. After the metal goes through the rollers, it's automatically cut to the right length.
The most common shape for corrugated material is the classic wavy style. However, different rollers can create many other shapes and sizes. For example, industrial buildings often use metal sheets with a trapezoidal (trapezoid-like) shape.
Many different metals are corrugated today. The most common ones are ferrous alloys (like stainless steel), aluminum, and copper. Ferrous alloys are used most often because they are affordable and easy to get. Corrugated sheets come in many thicknesses. They can be very thin, like 0.3 millimeters (0.012 inches), or quite thick, like 4.9 millimeters (0.1943 inches).
Other materials are also made with corrugations. These include thermoplastic and fiberglass-reinforced plastic sheets. Clear or see-through versions of these can let light shine through, which is useful for skylights.
Waves: Pitch and Depth
When we talk about the waves in corrugated iron, we use two terms:
- Pitch: This is the distance from the top of one wave to the top of the next wave.
- Depth: This is how tall the wave is, from the bottom of the dip to the top of the crest.
It's important for the pitch and depth to be very even. This makes it easy to stack the sheets for transport. It also helps them overlap neatly when you join two sheets together. The pitch can be anywhere from 25 millimeters (1 inch) to 125 millimeters (5 inches).
In the past, corrugated iron used for walls often had smaller waves (shorter pitch and depth) than roofing material. This was sometimes called "rippled" instead of "corrugated." However, almost all corrugated iron made today has the same pitch of 76 millimeters (3 inches).
There's even a special design of corrugated steel sheets called "Proster 21." These sheets have V-shaped dips that are 21 millimeters deep. They are used as formwork to help shape concrete.
Rust and How to Stop It
Even though the zinc coating (galvanising) helps stop steel from rusting, rust can still happen over time. This is especially true near the ocean, where salty air speeds up rust. It also happens in places where the rain is acidic.
However, even rusted corrugated steel roofs can last for many years. This is especially true if they are painted. The paint adds another layer of protection against the weather.
See also
- Chattel house
- Metal roof
- Nissen hut
- Quonset hut
- Tin tabernacle