Glassblowing facts for kids
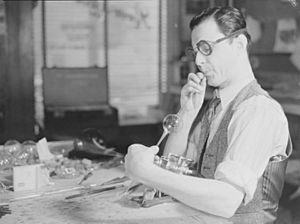
Glassblowing is an amazing way to shape hot, melted glass. You use a special tube called a blowpipe to puff air into the glass. This makes the glass expand into a bubble, like blowing a balloon! The person who does this is called a glassblower. Sometimes, people called lampworkers also shape glass. They use a torch for smaller items, like special lab equipment.
Contents
How Glassblowing Works
The Science Behind It
Glassblowing was invented around the 1st century BC. Before this, people didn't know you could inflate melted glass. This new idea used a special quality of glass: it can expand when air is blown into it.
Melted glass is like a very thick liquid. Its tiny parts are connected in a messy way. This makes the glass sticky enough to be blown. It also slowly gets harder as it cools down.
To make the glass even better for blowing, its ingredients were changed a little. Early glassblowers used less "natron," a substance that makes glass softer. Using less natron made the glass stiffer, which was perfect for blowing.
When you blow glass, the thinner parts cool faster than the thicker parts. They also become stickier. This helps the glass become a smooth, even thickness. It stops the thin spots from blowing out completely.
Glassblowers quickly learned many different ways to blow glass. The two main methods are free-blowing and mold-blowing.
Free-Blowing Technique
Free-blowing was the most popular way to shape glass for a very long time. It was used from the 1st century BC until the late 1800s. Even today, artists still use free-blowing to create beautiful glass art.
To free-blow, a glassblower blows short puffs of air into a blob of melted glass. This blob is called a "gather" and is at the end of the blowpipe. Blowing air creates a stretchy skin inside the glass blob. This skin matches the cool skin on the outside.
The glassblower can then quickly inflate the hot glass into a bubble. They can shape it into almost any form. They do this by turning the pipe, swinging it, and controlling the glass's temperature. They can make many different things, from drinking cups to window glass.
A famous example of free-blowing is the Portland Vase. This amazing vase was made during the Roman period. Experts have even tried to recreate it. They gathered blue glass for the vase's body. Then, they dipped it into hot white glass. The glassblower then blew the melted glass into a sphere. Finally, they stretched it into a vase shape with a layer of white glass over the blue.
Mold-Blowing Technique
Mold-blowing came after free-blowing, in the 1st century AD. In this method, a blob of melted glass is put on the end of the blowpipe. Then, it's blown into a mold made of wood or metal. The mold's design shapes the glass bubble. This means the glassworker's skill is less important for the final shape.
There are two main types of molds: single-piece molds and multi-piece molds. Single-piece molds let you pull the finished glass object straight up and out. These are often used for tableware or simple storage jars. Multi-piece molds are made of several parts that fit together. These allow for much more detailed shapes and designs on the glass.
The Roman leaf beaker, now in the J. Paul Getty Museum, was made using a three-part mold. This mold had a design of four vertical plants. Experts have tried to make similar mold-blown vessels. They found that metal molds, especially bronze, create clearer designs on glass than plaster or wood molds.
Mold-blowing made it possible to quickly produce many glass objects. This helped glass items become widely available to more people.
Modern Glassblowing
Raw materials turn into glass at about 2400°F (1315°C). At this heat, the glass glows almost white. Then, it's left to "fine out," which means tiny bubbles rise out of it. The working temperature is then lowered to about 2000°F (1093°C). At this point, the glass looks bright orange. Most glassblowing happens between 1600°F and 1900°F (871°C and 1037°C). "Soda-lime" glass can still be shaped at temperatures as low as 1350°F (732°C).
Glassblowing uses three main furnaces (special ovens). The first is simply called the furnace. It holds a pot of melted glass. The second is the glory hole. This is used to reheat the glass piece while the glassblower is working on it. The last furnace is called the lehr or annealer. It slowly cools the glass over several hours or even days. This slow cooling stops the glass from cracking or breaking due to sudden temperature changes. In the past, all three furnaces were part of one large structure, with cooler areas for each step.
Glassblowers use many tools. The main ones are the blowpipe, punty, bench, marver, blocks, jacks, paddles, tweezers, and special shears.
First, the tip of the blowpipe is heated. Then, it's dipped into the melted glass in the furnace. The melted glass "gathers" onto the blowpipe, like honey on a dipper. This glass is then rolled on the marver. A marver was traditionally a flat marble slab, but now it's usually a thick steel sheet. This rolling creates a cool skin on the outside of the glass blob and shapes it. Then, air is blown into the pipe to create a bubble. The glassblower can add more glass over this bubble to make a larger piece.
Once the piece is almost its final size, the bottom is finished. Then, the hot glass is attached to a metal rod called a punty. This helps move the hollow piece from the blowpipe. It also allows the glassblower to shape the top or opening of the piece.
The bench is where the glassblower works. It has a seat, a place for tools, and two rails. The blowpipe or punty rests on these rails while the glassblower works. Blocks are ladle-shaped tools made from wet wood. They are used like the marver to shape and cool the glass in the early stages. Wet newspaper pads can also be used by hand to shape the glass.
Jacks are like large tweezers with two blades. They are used to shape the glass later on. Paddles are flat pieces of wood or graphite. They are used to create flat areas, like the bottom of a vase. Tweezers help pick out details or pull on the glass. There are two main types of shears: straight shears and diamond shears. Straight shears are like strong scissors for making straight cuts. Diamond shears have blades that form a diamond shape when partly open. These are used to cut off extra glass.
Glassblowers can add patterns and colors in many ways. They might roll hot glass in colored powder or larger pieces of colored glass called frit. Very detailed patterns can be made using cane (rods of colored glass) and murrine (rods cut into slices to show patterns). These colored pieces can be laid out on a flat surface. Then, a bubble of melted glass is rolled over them to "pick them up." One very complex technique is "reticello." This involves making two bubbles from cane, twisting each in a different direction. Then, they are combined, and the final shape is blown.
Lampworkers usually work on a smaller scale. In the past, they used alcohol lamps and air from their breath or bellows to create a hot flame. They shaped pre-made glass rods and tubes. They made things like lab glassware, beads, and small glass sculptures. Today, modern lampworkers use flames from oxygen and propane or natural gas. This allows them to work with different types of glass, including the strong borosilicate glass used in science.
Images for kids
-
Roman blown glass hydria from Baelo Claudia (4th century AD)
See also
In Spanish: Vidrio soplado para niños