Cement facts for kids
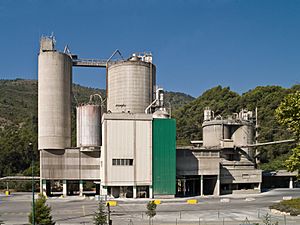
Cement is a special kind of glue that can stick other materials together. It's a powder that hardens on its own. The word "cement" comes from the Romans. They used "opus caementicium" to describe a strong building material. It was made from crushed rock and burnt lime. They added volcanic ash and ground bricks to make it even stronger. This strong mix was later called "cementum."
The most important use for cement is making mortar and concrete. Mortar is used to hold bricks or stones together. Concrete is a very strong building material. It's made by mixing cement with sand, gravel, and water. This creates a material that lasts a long time, even in different weather.
It's easy to confuse cement with concrete, but they are not the same! Cement is just the dry powder. It's like the flour in a cake. Concrete is the finished mix. It's like the whole cake, with all the ingredients mixed together. When you add water and other things to cement, it becomes concrete, especially when you add sand and gravel.
Contents
The Story of Cement
Ancient Builders and Cement
People aren't sure exactly where the idea of mixing lime with volcanic ash or ground bricks first came from. This mix made a special kind of cement that hardened even underwater. This type of cement was used a lot by Roman engineers. They used natural materials like volcanic ash or man-made ones like ground pottery.
Many amazing Roman buildings still stand today because of this strong concrete. Think of the huge dome of the Pantheon in Rome. Or the massive Baths of Caracalla. The Romans also used this strong cement for their huge system of Roman aqueducts. After the Roman Empire, using strong concrete for big buildings mostly stopped in Europe. But weaker versions were still used inside stone walls.
How Modern Cement Was Invented
A big step in making modern cement happened with John Smeaton. He was building the third Eddystone Lighthouse in England (1755-1759). He needed a special mortar that would harden quickly between high tides. Smeaton studied different limes. He found that the best ones came from limestone with more clay in it.
Later, in the early 1800s, Louis Vicat discovered the same thing. He figured out how to mix chalk and clay. Then he burned them to make an "artificial cement" in 1817. Around the same time, James Frost in Britain made something similar. He called it "British cement."
In 1824, Joseph Aspdin patented his own material. He named it "Portland cement." This was because its color looked like the famous Portland stone.
Early cements had some problems. They set too fast, so workers didn't have enough time to use them. They also didn't get strong very quickly. This meant builders had to wait weeks before removing wooden supports. These early cements got their strength from a material called "belite," which works slowly. They were burned at lower temperatures. This meant they didn't have "alite," which makes modern cements strong fast.
The first cement that consistently had alite was made by Joseph Aspdin's son, William. This happened in the early 1840s. This was the start of what we call "modern" Portland cement. William kept his methods secret. But his cement, made in Northfleet, Kent, was truly an alite-based cement. Others like Vicat and I C Johnson also helped. Vicat explained the chemistry, and Johnson showed how important it was to heat the mix very hot in a kiln.
William Aspdin's new cement was harder to make. It needed more lime and much higher heat. This used more fuel. Also, the super-hard material that came out, called clinker, wore down the grinding machines quickly. So, it cost more to make. But this new cement set at a good speed and got strong very fast. This opened up a huge market for using cement in concrete. From 1850 onwards, concrete building grew quickly. Portland cement soon became the most important type of cement.
Cement's Impact on Our World
Making cement affects the environment in many ways. It can cause air pollution from dust and gases. There's also noise and shaking from machines and blasting in quarries. Quarries also change the look of the countryside.
Today, factories use special equipment to reduce dust. They also have systems to capture and clean exhaust gases. When quarries are no longer used, they are often returned to nature. Or they are replanted with new trees and plants.
Local Effects of Cement Production
Cement factories can have both good and bad effects on local areas. On the good side, they create jobs. They also bring business opportunities for people living nearby. This is especially true in faraway places in developing countries. There might not be many other ways to earn money there.
On the negative side, factories can disturb the landscape. There can be dust and noise. Quarrying for limestone, which is a main material for cement, can also harm local plants and animals.
Images for kids
-
Calcium oxide powder. It's made by heating calcium carbonate to very high temperatures.
-
William Aspdin is known for inventing "modern" Portland cement.
See also
In Spanish: Cemento para niños