Microwave popcorn facts for kids
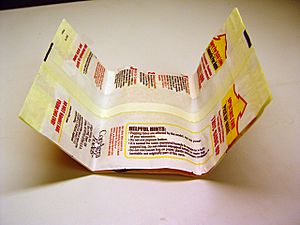
Microwave popcorn is a super easy snack! It comes with unpopped popcorn kernels inside a special, sealed paper bag. You just put the bag in a microwave oven to heat it up.
Besides the dried corn, these bags usually have cooking oil that gets solid when it's cool. They also contain seasonings, like salt, and natural or artificial flavorings to make it taste good. Lots of different companies make microwave popcorn with many exciting flavors!
Contents
How Microwave Popcorn Works
When you put the bag in the microwave, it's usually folded. As the kernels heat up, they create steam inside the bag. This steam builds up pressure, which makes the bag puff up and inflate.
The Special Bag Design
Microwave popcorn bags are made to stop the popped corn from burning. This burning happens if the popcorn gets too hot, over 300 degrees Fahrenheit.
The bags have a special part called a "susceptor." This is usually a thin, shiny film stuck to the paper. It soaks up the microwave energy and focuses the heat. This helps to spread the heat evenly to the flavor coating on the kernels. This way, all the unpopped kernels get coated well before they pop, making sure your popcorn tastes great all over!
Why Some Kernels Don't Pop
Sometimes, a popcorn kernel won't pop. This can happen if its outer shell is damaged, letting the steam escape. These unpopped kernels are often called "old maids."
The first special popcorn bag design was created by an American company called General Mills in 1981.
Important Safety Tips
It's important to be careful when cooking microwave popcorn. The cooking time on the package might not be perfect for every microwave oven. If you set a timer and walk away, your popcorn could burn and make a lot of smoke.
It's always best to stay near the microwave while your popcorn is cooking. Listen carefully! When the popping sounds slow down to only a few seconds between pops, it's time to take the popcorn out. This helps prevent burning.
Environmental Concerns
In recent years, people have become more worried about the waste from microwave popcorn bags and their impact on the environment. Studies show that food packaging makes up a big part of all packaging waste.
Also, some materials used to coat microwave popcorn bags can be harmful to the environment. Scientists have found certain chemicals in these bags, like perfluorinated compounds (PFCs). These PFCs can stay in the environment for a very long time and might be harmful. Some well-known PFCs are called perfluorooctanesulfonic acid (PFOS) and perfluorooctanoic acid (PFOA). These chemicals have been found in water, soil, air, and even in wildlife.
To help the environment, many ways have been developed to remove these PFCs from water.
Harmful Chemicals in Bags
Scientists have found many PFCs in microwave popcorn bags. These chemicals are used to make the bags resistant to oil and moisture. PFOA and PFOS are the most studied PFCs.
PFCs are not easily broken down by nature and can stay in the environment for a long time. They can also build up in living things, which might cause problems for animals and people. For example, some studies have shown that PFOA might be linked to kidney cancer in people living near chemical factories.
Because of these concerns, major companies in the U.S. agreed to stop making PFOA by the end of 2015. Also, the U.S Food and Drug Administration (FDA) stopped allowing certain PFCs in food packaging in 2016.
However, even though PFOA and PFOS production went down, other similar chemicals are still used in food packaging. Some of these chemicals can break down into PFCs, which could still add to the amount of PFCs in the environment.
How Bags Affect the Environment
PFCs are very strong chemicals that don't easily break down naturally. Once they get into the environment, they can become pollutants. Evidence shows that water, air, soil, and wildlife around the world have been affected by PFCs.
Because so many microwave popcorn bags are made, they are a big source of these PFCs in the environment. When these coated paper bags are thrown away, PFCs can get into wastewater and soil near disposal sites.
Cleaning Up the Environment
To reduce the harmful effects of PFCs, scientists have created many ways to remove them from water. These methods include things like using special materials to soak them up, filtering them out, or using light or sound to break them down.
Some microwave ovens even have a special popcorn setting. This setting uses pre-set times and power levels, or it might use sensors to know when the popping has finished.