Six Sigma facts for kids
Six Sigma (which looks like 6σ) is a special way of using tools and methods to make things better. It was first started by an engineer named Bill Smith at Motorola in 1986.
Six Sigma helps companies make their products and services much better. It finds and fixes problems that cause mistakes or "defects." It also helps make sure things are always done the same way, reducing differences. This is done by using smart tools and hiring experts in Six Sigma. Each Six Sigma project has clear goals, like making customers happier or reducing waste.
The name Six Sigma comes from statistics. It refers to how few mistakes a process makes. Imagine a perfect line of products; Six Sigma aims for almost no mistakes at all.
Contents
How Six Sigma Started
Motorola was the first company to use Six Sigma. They wanted their manufacturing to be super good, aiming for "six sigma" quality. Motorola even registered Six Sigma as a special name in 1991. By 2005, Motorola said Six Sigma saved them over $17 billion!
Other big companies like Honeywell and General Electric also started using Six Sigma early on. In 1995, Jack Welch, the CEO of GE, made Six Sigma a key part of their business plan. By 1998, GE reported saving $350 million because of Six Sigma. This helped Six Sigma become very popular. By the late 1990s, many large companies were using it to save money and improve quality.
More recently, some people have combined Six Sigma with another method called lean manufacturing. This new way is called Lean Six Sigma. Lean manufacturing helps reduce waste and improve how things flow. Six Sigma focuses on reducing mistakes and making things consistent. Together, they aim to make businesses excellent.
In 2011, the International Organization for Standardization (ISO) even made a standard for how Six Sigma processes should work.
What Does "Six Sigma" Mean?
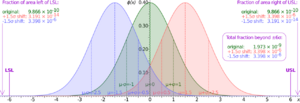
The name "Six Sigma" comes from statistics. It's about how well a process can make things without mistakes. When a process has "six sigma quality," it means it makes very, very few errors.
Think of it like this: if you make a million things, a "six sigma" process would have fewer than 3.4 mistakes. That's super good! This idea includes a small "shift" that experts expect to happen over time.
The Greek letter σ (sigma) stands for "standard deviation." This is a way to measure how much things vary or spread out. If a process has a small sigma, it means everything is very consistent. Six Sigma aims for very little variation.
What Six Sigma Believes In
Six Sigma teaches a few main ideas:
- It's super important to always work on making processes stable and predictable. This means reducing how much things vary.
- You can define, measure, analyze, improve, and control how things are made or how businesses work.
- To truly make things better for a long time, everyone in the company, especially the leaders, needs to be committed.
What makes Six Sigma different from older ways of improving quality?
- It focuses on getting real, measurable money savings.
- It really emphasizes that leaders must be involved and support the effort.
- It insists on making decisions based on real facts and numbers, not just guesses.
Both Six Sigma and lean management have similar tools. But lean management mainly focuses on getting rid of waste and making things more efficient. Six Sigma focuses on getting rid of mistakes and making things consistent. Both use data, but Six Sigma relies a lot on very accurate data.
The main goal of Six Sigma is to make all processes better. Companies decide how good each important process needs to be. Then, they work to reach that level.
How Six Sigma Projects Work
Six Sigma projects usually follow two main methods, each with five steps. These methods are inspired by W. Edwards Deming's Plan–Do–Study–Act Cycle.
- DMAIC (pronounced "duh-may-ick") is used when you want to make an existing process better.
- DMADV (pronounced "duh-mad-vee") is used when you want to create new products or processes.
DMAIC Steps
The DMAIC method has five phases:
- Define: Figure out what the system is, what customers need, and what the project goals are.
- Measure: Collect information about how the current process works. See how well it's doing now.
- Analyze: Look at the information to find out why problems are happening. Try to find the main cause of any mistakes.
- Improve: Make changes to the process based on what you found. You might test new ideas or make things "mistake-proof."
- Control: Keep an eye on the new process to make sure it stays good. This helps prevent new mistakes from happening. You keep doing this until the quality is just right.
Some companies add a "Recognize" step at the beginning, making it RDMAIC. This is about picking the right problem to work on.
DMADV Steps
DMADV is also known as DFSS (Design For Six Sigma). Its five phases are:
- Define: Set goals for a new design that match what customers want and what the company needs.
- Measure: Figure out what qualities are most important to customers. Check how well products or processes can meet these needs.
- Analyze: Come up with different ideas for the design.
- Design: Choose the best design idea based on your analysis.
- Verify: Test the new design. Do small trial runs and then put the new process into action.
Six Sigma Experts
Six Sigma has a special way of organizing people who work on quality. It uses a ranking system, a bit like martial arts belts, to show different levels of expertise.
Here are the main roles in Six Sigma:
- Executive Leadership: These are the top bosses, like the CEO. They set the big picture for Six Sigma and give others the power and resources to make changes.
- Champions: These are managers who lead Six Sigma efforts across the company. They also guide the Master Black Belts.
- Master Black Belts: These are in-house Six Sigma coaches. They spend all their time on Six Sigma, helping Champions and guiding Black Belts and Green Belts. They make sure Six Sigma is used correctly everywhere.
- Black Belts: They work on specific Six Sigma projects full-time. They focus on carrying out the projects and leading special tasks.
- Green Belts: These employees work on Six Sigma projects while also doing their regular jobs. They get guidance from Black Belts.
People in these roles get special training to make sure they follow the Six Sigma methods and use data correctly. Some companies also have "yellow belts" (basic training) or "white belts" (know the basics but don't join projects).
Getting Certified
Companies like General Electric and Motorola created their own Six Sigma certification programs. Now, many organizations offer Six Sigma certifications. The requirements for Green Belt and Black Belt can be different. Some just need you to take a course and complete a project. There isn't one single official group that gives all certifications.
Tools and Methods Used
Six Sigma uses many different tools to help improve processes. These tools are often used in other quality management programs too.
Here are some of the main tools:
- 5 Whys: Asking "why" five times to find the root cause of a problem.
- Cause & effects diagram (also called fishbone diagram): Helps map out all possible causes for a problem.
- Control chart: A graph that shows if a process is staying in control or if something unusual is happening.
- Design of experiments: A way to test different factors to see how they affect a process.
- Histograms: Bar graphs that show how often different values appear.
- Pareto analysis: Helps find the most important causes of problems (the "vital few").
- Root cause analysis: Finding the very first reason a problem occurred.
- SIPOC analysis: A tool to map out a process by looking at Suppliers, Inputs, Process, Outputs, and Customers.
- Value stream mapping: A way to visualize all the steps in a process to find waste.
Where Six Sigma is Used
Six Sigma is often used in large companies. However, many of its tools can also help smaller businesses.
In Manufacturing
Six Sigma started in manufacturing at Motorola. Since then, many other big companies have saved a lot of money using it. For example, Johnson & Johnson reported saving $600 million, and Texas Instruments saved over $500 million. Companies like Sony and Boeing have also used it to reduce waste.
In Engineering and Construction
Six Sigma helps in construction too. For example, a study found that a construction company reduced building time by 26.2% and waste by 67% after using Six Sigma. Bechtel Corporation, a huge engineering company, saved over $200 million by using Six Sigma to prevent mistakes and rework.
In Finance
Six Sigma has helped banks and financial companies. It can make sure money is given out correctly, reduce bank fees, and improve how reports are made. Bank of America said Six Sigma helped them make customers 10.4% happier and reduced customer problems by 24%. American Express used it to stop people from not getting their new credit cards.
In Supply Chain
In the supply chain, Six Sigma helps make sure products get to customers on time and with high quality. It can improve how products are moved and delivered, making sure they are defect-free and arrive when promised.
In Healthcare
Healthcare is a field where mistakes can be very serious, so Six Sigma is a good fit. It helps reduce extra costs from equipment, make healthcare delivery more efficient, and improve billing. For example, the MD Anderson Cancer Center increased patient examinations by 45% and cut patient preparation time by 40 minutes in some cases.
Lean Six Sigma was also adopted by Stanford hospitals in 2003 and Red Cross hospitals in 2002.
Why Some People Criticize Six Sigma
Even though Six Sigma has many fans, some projects don't succeed. In 2010, a newspaper reported that over 60% of projects fail.
Here are some common reasons why projects might not work well:
- Leaders don't fully support or get involved.
- Not enough training or resources (money, tools, people).
- Picking the wrong projects or not connecting them to company goals.
- People don't like change.
- Poor communication.
- Not understanding the tools well enough.
Other criticisms include:
Not New Ideas
Some experts say that Six Sigma isn't really new. They say it's just a new name for older quality improvement ideas. They also point out that the "belt" system is just a fancy way to name specialists, which isn't a new idea either.
Too Much Focus on Statistics
Some critics say Six Sigma relies too much on numbers and strict methods. They argue that it focuses a lot on reducing variation but less on designing things to be strong and reliable from the start. They also worry that using too many statistical tests can lead to mistakes in conclusions.
Can Stop New Ideas
Some people believe that Six Sigma can stop new and creative ideas, especially in research. They say that too many rules and measurements can make it hard for people to brainstorm freely or discover new things by accident. For example, at 3M, a company known for inventing new products, Six Sigma was removed from the research department because it was seen as stifling creativity.
Not Enough Proof
Some critics say that while Six Sigma claims to be based on science, many of the success stories aren't written down in a detailed, academic way. They wonder if companies are truly improving or just getting good at telling stories about success.
Images for kids
- Design for Six Sigma
- DMAIC
- Kaizen – a focus on always making things better
- Lean Six Sigma
- Lean manufacturing
- Quality management
- Total quality management
- W. Edwards Deming
See also
In Spanish: Seis Sigma para niños