Solar thermal energy facts for kids
Solar thermal energy (often called STE) is a way to use the sun's energy to make heat. This heat can be used in homes, businesses, and factories.
Solar thermal collectors are like special panels that collect sunlight. They are grouped into three types:
- Low-temperature collectors: These are usually simple panels without glass. They are often used to heat swimming pools or to warm the air for ventilation.
- Medium-temperature collectors: These are usually flat panels with glass. They are used to heat water or air for homes and businesses.
- High-temperature collectors: These use mirrors or lenses to focus sunlight, making it very hot. They are used in factories for heat up to 300°C or to make electricity. When used for factory heat, it's called Concentrated Solar Thermal (CST). When used to make electricity, it's called Concentrated Solar Power (CSP).
The biggest solar thermal power plants are in the Mojave Desert in California and Nevada, USA. Some examples are Ivanpah Solar Power Facility (377 MW), Solar Energy Generating Systems (354 MW), and Crescent Dunes (110 MW). Spain is another big user of solar thermal power, with plants like Solnova Solar Power Station (150 MW), Andasol solar power station (150 MW), and Extresol Solar Power Station (100 MW).
Contents
History of Solar Heat
In 1878, a scientist named Augustin Mouchot showed off a solar collector that could make ice cream in Paris! The first large solar thermal system was built around 1910 in the Sahara desert by Frank Shuman. It used sunlight to create steam, which powered an engine. However, because gasoline engines became popular and easier to use, this project was stopped. But the idea came back many years later!
Using Solar Heat for Homes and Buildings
Systems that use low-temperature solar energy collect heat, store it (for a short time or even for different seasons), and then spread it around a building or a group of buildings. Some systems work on their own (passive), while others need a little extra energy to run (active).
Heating is the most common use, but solar energy can also be used for cooling! Special machines called absorption or adsorption chillers can use heat from the sun to cool a building. It's cool because the hotter the sun shines, the more cooling power these machines have. In 1878, Auguste Mouchout even made ice using a solar steam engine connected to a refrigerator.
In the United States, heating, ventilation, and air conditioning (HVAC) systems use a lot of energy in buildings. Solar heating, cooling, and ventilation can help save some of that energy. A popular way to heat buildings with solar energy is using "transpired solar air collection systems." These systems connect to a building's HVAC. By 2015, over 500,000 square meters of these panels were being used in North America.
In Europe, since the 1990s, many large solar-thermal systems have been built to heat entire neighborhoods. Some of the biggest are about 10,000 square meters, providing heat for many homes.
How Low-Temperature Collectors Work
Glazed solar collectors are mainly for heating spaces. They take air from inside a building, heat it up in a solar panel, and then send the warm air back into the building. These systems only work when the air in the collector is warmer than the room. Most glazed collectors are used in homes.
Unglazed solar collectors are mostly used to warm up fresh air coming into large buildings like factories or schools. They turn parts of a building's walls into simple, effective solar collectors. These are also called "transpired solar panels" or "solar walls." They use a painted metal sheet with tiny holes that acts as the building's outer wall. Sunlight heats this metal. Air is pulled through the holes and behind the metal, where it gets warm before going into the building's ventilation system.
A Trombe wall is a clever way to heat and cool a building naturally. It's a wall facing the sun with a space between it and a window. During the day, the sun heats the wall, which warms the air in the space. This warm air rises and flows into the building through vents, pulling cooler air in from the bottom. At night, the wall slowly releases its stored heat into the building.
Solar roof ponds, developed by Harold Hay in the 1960s, are another way to use solar energy for heating and cooling. Imagine a water-filled bag on your roof with a movable cover. To heat, you uncover the bag during the day so the sun warms the water. At night, you cover it to keep the heat in. To cool, you cover the bag during the day to keep the sun out, and uncover it at night so the water can release heat to the cool night air, drawing heat from inside the house.
Solar air collectors are more popular in the USA and Canada for heating buildings than solar liquid collectors. This is because most buildings already have air ventilation systems. The two main types are glazed (with glass) and unglazed (without glass).
In 2007, out of all the solar thermal collectors made in the US, most were low-temperature ones. These are mainly used for heating swimming pools, but can also heat spaces. They can use either air or water to move the heat.
Storing Heat for Buildings
There are technologies that can store heat for many months. This means solar heat collected in the summer can be used to heat buildings all winter long! This is called seasonal thermal energy storage (STES). Countries like Denmark, Germany, and Canada have made great progress with STES. For example, the Drake Landing Solar Community in Canada gets 97% of its heating needs from the sun all year round! Heat can be stored in underground water layers (aquifers), in rock, in large gravel pits, or in big insulated water tanks buried underground.
Storing heat between seasons: Solar heat can be stored for a long time in underground water, rock formations, large pits, or big insulated tanks.
Short-term heat storage: Materials like stone, concrete, and water can store solar energy during the day and release it when it gets cooler. Using these "thermal mass" materials correctly can help keep temperatures comfortable and save energy.
Solar-Powered Cooling
By 2011, there were about 750 cooling systems that used solar-powered heat pumps worldwide. This market was growing fast! It's still a special market because it can be expensive, and it works best where there are many hours of sunshine for cooling. However, the cost of building these systems dropped by about 50% between 2007 and 2011.
Solar Heat for Ventilation
A solar chimney (or thermal chimney) is a natural ventilation system. It's a hollow, heat-absorbing structure that connects the inside and outside of a building. As the chimney gets warm, the air inside heats up and rises, pulling fresh air through the building. These systems have been used since Roman times and are still common in the Middle East.
Heat for Industrial Processes
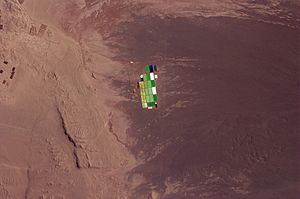
Solar process heating systems provide large amounts of hot water or heat for non-residential buildings, like factories.
Evaporation ponds are shallow ponds that use the sun to dry out water, leaving behind dissolved solids like salt. Getting salt from seawater using evaporation ponds is one of the oldest uses of solar energy! Today, they are also used to concentrate solutions in mining or to clean up waste water. These ponds are one of the biggest commercial uses of solar energy today.
Unglazed transpired collectors (the perforated walls we talked about earlier) are used to preheat air for ventilation. They can also be put on roofs for year-round use. They can raise the air temperature by up to 22°C and deliver air at 45-60°C. They pay for themselves quickly (in 3 to 12 years) compared to glazed systems. By 2015, over 4000 of these systems were installed worldwide. One in Costa Rica (860 m²) dries coffee beans, and another in India (1300 m²) dries marigolds.
A food factory in California uses special curved mirrors (parabolic troughs) to make steam for its manufacturing process. This system, covering 5,000 square meters, is expected to provide a lot of heat each year.
Medium-Temperature Collectors
These collectors can provide about half or more of the hot water needed for homes and businesses. In the US, a typical system costs around $4000-$6000. The government often gives tax credits, which can help reduce the cost. For a typical home, the system can pay for itself in four to nine years. These systems are quite easy to install.
Medium-temperature systems can use different designs:
- Pressurized glycol systems
- Drain-back systems
- Batch systems
- Newer low-pressure systems that can handle freezing, using plastic pipes with water and solar-powered pumps.
These systems have low maintenance costs and can save a household money on energy bills. Using solar water heating can also reduce carbon dioxide (CO2) emissions, which is good for the environment.
Solar Drying
Solar thermal energy is great for drying wood for building or for fuel like wood chips. It's also used to dry food products like fruits, grains, and fish. Drying crops with solar energy is good for the environment and saves money, which can make products cheaper for buyers. Simple, low-cost air collectors made from black fabrics are used for solar drying.
Cooking with the Sun
Solar cookers use sunlight to cook food, dry it, or clean water by heating it to kill germs. Using solar cookers saves money on fuel and reduces smoke, which improves air quality.
The simplest solar cooker is the box cooker, first made in 1767. It's an insulated box with a clear lid. These can cook even on partly cloudy days and reach temperatures of 50–100°C.
Concentrating solar cookers use mirrors to focus sunlight onto a cooking pot. The most common types use flat, disc, or parabolic trough mirrors. These cook faster and hotter (up to 350°C) but need direct sunlight.
The Solar Kitchen in Auroville, India, uses a special "solar bowl." This giant bowl-shaped mirror stays still, but a receiver inside moves to follow the sun's focus. It reaches 150°C and makes steam to cook 2,000 meals daily.
Many other solar kitchens in India use a "Scheffler reflector." This mirror, invented in 1986, is a parabolic dish that tracks the sun. It can change its shape to adjust to the sun's position throughout the year. Scheffler reflectors have a fixed cooking spot, making them easy to use, and can reach very high temperatures (450-650°C). The world's largest Scheffler reflector system in India can cook up to 35,000 meals a day!
Making Clean Water (Distillation)
Solar stills can make drinking water in places where clean water is hard to find. The sun's energy heats water in the still, turning it into steam. The steam then rises and condenses (turns back into liquid water) on the underside of a glass cover, dripping down as clean, purified water.
High-Temperature Collectors
For temperatures below about 95°C (like for home heating), flat-plate collectors are usually used. But these don't get hot enough (above 200°C) to efficiently make electricity.
To make electricity efficiently, solar thermal power plants need much higher temperatures. They do this by using mirrors or lenses to focus sunlight, a method called Concentrated Solar Power (CSP). Higher temperatures mean the power plant can be smaller and use less land for the same amount of power, which is better for the environment and costs less.
As the temperature increases, different ways of making electricity become possible. Up to 600°C, steam turbines (like those in regular power plants) can be used efficiently. Above 600°C, gas turbines might be even better. Very high temperatures are tricky because they need special materials. One idea is to use liquid salts heated to 700-800°C to get over 50% efficiency. Higher temperatures also mean less water is needed for cooling, which is important in deserts where these plants are often built.
The first large CSP plants were built in the 1980s. The biggest ones today are the 370 MW Ivanpah Solar Power Facility (started in 2014) and the 354 MW SEGS plant, both in the Mojave Desert in California. Most other large CSP plants (100 MW or more) are in the United States or Spain.
A big advantage of CSP is that it can store heat. This means the plant can make electricity even when the sun isn't shining, like at night or on cloudy days. Since electricity demand is often highest in the evening, many CSP plants store heat for 3 to 5 hours. Storing heat is much cheaper and more efficient than storing electricity. This allows CSP plants to provide reliable power day and night. They can even have a backup system that uses natural gas if needed.
CSP plants use a lot of copper in their wiring, grounding, and motors for tracking mirrors and pumping fluids.
The main challenges for large CSP plants are their cost, how they look, and the amount of land they use, as well as the power lines needed to connect them. Even though only a small part of the desert is needed to power the world, a large area must be covered with mirrors to get a lot of energy. Making the designs simpler can help reduce costs.
Compared to fossil fuel power plants, which need land for drilling, mining, and transportation, large solar power plants actually use land very efficiently. The government has leased much more land for oil and gas than for solar development.
How High-Temperature Systems Work
The sun moves across the sky during the day. For systems that don't focus sunlight much (and don't get super hot), the mirrors might not need to move. But for systems that focus sunlight a lot, the mirrors or lenses must move to follow the sun. This "tracking system" adds to the cost and complexity. Different designs handle this in different ways.
Parabolic Trough Designs
Parabolic trough power plants use long, curved mirrors shaped like a U. These mirrors reflect direct sunlight onto a glass tube that runs along the middle of the trough. This tube contains a fluid and is at the "focal point" where all the sunlight is concentrated. The trough is curved in one direction and straight in the other. To follow the sun's daily movement, the trough tilts from east to west. However, it doesn't need to adjust for seasonal changes in the sun's height, as the light still hits the tube. The tube might be inside a vacuum chamber to reduce heat loss.
A special fluid (called heat transfer fluid) flows through the tube and gets very hot. This fluid can be synthetic oil, molten salt, or pressurized steam. The hot fluid then goes to a "heat engine" (like a turbine) where about a third of its heat is turned into electricity.
Large parabolic trough systems have many of these troughs lined up in parallel over a big area. Since 1985, the Solar Energy Generating Systems (SEGS) in California has been using this technology. It's one of the most proven CSP technologies because it has been used for so long.
The SEGS system has nine plants with a total power of 354 MW. It was the world's largest solar power plant for many years. Another plant is Nevada Solar One (64 MW). The Andasol solar power stations in Spain (150 MW total) use heat storage, which means they can store heat and use it later to make electricity, even at night. This allows them to use the steam turbine more effectively. The 280 MW Solana Generating Station in Arizona, which started in 2013, can store power for 6 hours.
Enclosed Trough Systems
The enclosed trough design puts the solar thermal system inside a greenhouse-like building. This glasshouse protects the system from weather elements that could harm it or make it less efficient.
Lightweight, curved mirrors hang inside the glasshouse. A tracking system moves these mirrors to follow the sun and focus its light onto a network of steel pipes. Steam is made directly as water flows through these pipes, without needing extra heat exchangers.
The steam then goes into the existing steam system, for example, to help extract oil from the ground. Protecting the mirrors from wind allows them to reach higher temperatures and prevents dust from building up. One company, GlassPoint Solar, says its technology can produce heat for about $5 per unit of energy in sunny areas, which is cheaper than other solar thermal methods.
GlassPoint's system is used at the Miraah facility in Oman, and a new project is planned for California.
Power Tower Designs
Solar power towers (also called 'central tower' or 'heliostat' power plants) use thousands of tracking mirrors (called heliostats) spread over a large area, often two square miles. A tall tower stands in the middle of this field. The heliostats focus concentrated sunlight onto a receiver at the top of the tower. Inside the receiver, the concentrated sunlight heats molten salt to over 538°C (1000°F). This hot molten salt then flows into a storage tank, where it stays hot (98% thermal efficiency) and can be pumped to a steam generator. The steam then powers a standard turbine to make electricity. This process is similar to a coal power plant, but it uses clean solar energy.
The advantage of power towers over parabolic troughs is the higher temperature they reach. Higher temperatures mean electricity can be made more efficiently, and heat can be stored more cheaply for later use. Also, the ground doesn't need to be perfectly flat. A power tower could even be built on a hillside. The mirrors can be flat, and all the plumbing is in the tower. The downside is that each mirror needs its own two-axis tracking system, which can be more complex than the single-axis tracking used for many mirrors in a parabolic trough system.
Studies have shown that power towers might produce electricity at a lower cost than parabolic troughs in the future. The first commercial power tower was PS10 in Spain (11 MW), finished in 2007. Since then, many have been built, including the Ivanpah Solar Power Facility in California, which has three towers and generates 392 MW, making it the largest solar power tower plant when it opened in 2013.
Dish Designs
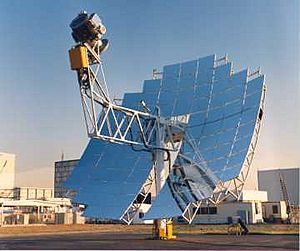
Dish Stirling systems are known for being very efficient (around 30%, compared to solar panels at 15%). They are predicted to be one of the cheapest renewable energy sources in sunny, desert areas. A dish Stirling system uses a large, curved, parabolic dish (like a satellite TV dish) to focus all the sunlight onto a single point above the dish. A receiver at this point captures the heat and turns it into useful energy. Usually, the dish is connected to a Stirling engine, which creates motion that can be turned into electricity by a generator.
In 2005, a company called Southern California Edison agreed to buy 20,000 solar-powered Stirling engines to generate 500 megawatts of electricity. In 2010, the first demonstration plant using this technology opened in Arizona. In 2015, a Swedish company called Rispasso Energy reported that its Dish Stirling system being tested in the Kalahari Desert in South Africa showed 34% efficiency.
Fresnel Technologies
A linear Fresnel reflector power plant uses many long, narrow, slightly curved (or even flat) mirrors to focus light onto one or more long receivers positioned above the mirrors. A small curved mirror can be added on top of the receiver to focus the light even more. These systems aim to be cheaper by sharing a receiver among several mirrors, while still using a simple line-focus design with one axis for tracking. This is similar to the trough design. The receiver stays still, so no moving fluid connections are needed. The mirrors are also simpler to build because they don't have to support the receiver.
Prototypes of Fresnel lens concentrators have been made for collecting heat. While full-scale thermal systems using Fresnel lenses are not common, products that combine Fresnel lenses with solar panels are available.
MicroCSP
MicroCSP is used for smaller power plants (1 MW to 50 MW), for industrial heat applications, and when a lot of hot water is needed, like for resort swimming pools, water parks, or for cleaning and distillation.
Enclosed Parabolic Trough
The enclosed parabolic trough solar thermal system puts all its parts inside a greenhouse-like glass building. This protects the system from weather that could make it less reliable or efficient. This protection also includes nightly cleaning of the glass roof with automated washing systems. Lightweight, curved mirrors hang from the ceiling by wires. A tracking system moves the mirrors to get the most sunlight. The mirrors focus the sunlight onto a network of stationary steel pipes. Water is pumped through these pipes and boils to make steam when the sun is intense. This steam can then be used for industrial processes. Protecting the mirrors from wind helps them reach higher temperatures and stops dust from building up.
How Heat is Collected and Exchanged
Heat in a solar thermal system follows five main rules:
- Heat gain: How much heat is collected from the sun.
- Heat transfer: How heat moves from one place to another.
- Heat storage: How heat is kept for later use.
- Heat transport: How heat is moved from the collector to storage or where it's needed.
- Heat insulation: How heat is prevented from escaping.
Heat is the amount of thermal energy an object has, based on its temperature, mass, and how much heat it can hold (specific heat). Solar thermal power plants use special devices called heat exchangers that are designed to move heat efficiently. Copper is often used in these heat exchangers because it conducts heat very well, resists rust, and is strong. Copper is found in the parts that collect heat and in the pipes and heat exchangers for water tanks.
Heat gain happens when the system absorbs heat from the sun. Solar thermal systems trap heat using the greenhouse effect. This means a special surface lets short-wave sunlight in but traps the longer-wave heat and infrared radiation that are produced when the light hits an "absorber plate." Fluid, usually water, in tubes within the absorber collects this trapped heat and moves it to a heat storage tank.
Heat moves in two ways: by conduction or convection. When water is heated, energy moves through it by conduction. The hot water molecules move faster and spread out, becoming lighter than the cold water. This hot water rises, and cooler water sinks, creating a convection current that spreads the heat. Heat moves from the collector plates to the fluid by conduction. The heated fluid then travels through pipes to the heat storage tank. Inside the tank, heat spreads through the storage material by convection.
Heat storage allows solar thermal plants to make electricity even when the sun isn't shining. Heat is stored in an insulated tank during the day and used to generate power at night. The faster heat moves, the bigger the temperature difference between the hot and cold parts.
Heat transport is simply moving the heat from the solar collector to the storage tank. Heat insulation is very important for both the pipes and the storage tank. It stops heat from escaping, which means less energy is lost and the system works more efficiently.
Storing Heat for Power Plants
Thermal energy storage lets a solar thermal plant make electricity at night or on cloudy days. This means solar power can be used for "baseload" power (always on) as well as "peak power" (when demand is highest). This can help replace power plants that use coal or natural gas. Also, it means the power plant can be used more often, which saves money. Even short-term storage can help smooth out the "duck curve" – the rapid change in power needed from the grid when the sun sets and solar power drops quickly.
Heat is transferred to a special storage material in an insulated tank during the day and used to make power at night. Materials used for heat storage include pressurized steam, concrete, special "phase change materials," and molten salts (like calcium, sodium, and potassium nitrate).
Steam Storage
The PS10 solar power tower stores heat in tanks as pressurized steam. This steam can be used for about an hour. It's thought that it could store heat for longer, but this hasn't been shown in a working power plant yet.
Molten Salt Storage
Molten salt is used to store heat in solar power tower systems because it's liquid at normal pressure, cheap to store heat, works well with steam turbines, and isn't flammable or toxic. Molten salt is also used in other industries to move heat around.
The first common molten salt mixture was 60% sodium nitrate and 40% potassium nitrate. This mixture melts at 220°C (430°F) and is kept liquid at 290°C (550°F) in an insulated tank. Other salts, like calcium nitrate, can lower the melting point, allowing more energy to be taken out before the salt freezes.
This solar power system can make power in cloudy weather or at night using the heat stored in the hot salt tank. The tanks are insulated and can store heat for about a week. Tanks big enough to power a 100-megawatt turbine for four hours would be about 9 meters (30 feet) tall and 24 meters (80 feet) wide.
The Andasol solar power station in Spain was the first commercial solar thermal power plant to use molten salt for heat storage and nighttime power generation. It started in March 2009. In 2011, another plant in Spain, Torresol's 19.9 MW plant, made history by generating electricity non-stop for 24 hours using molten salt heat storage.
In January 2019, a 100 MW molten salt tower solar power plant in China started operating. It has an 11-hour molten salt heat storage system and can generate power for 24 hours straight.
Phase-Change Materials for Storage
Phase Change Materials (PCMs) are another way to store energy. They can store heat more efficiently. PCMs can be organic (from living things) or inorganic (not from living things). Organic PCMs are not corrosive, don't freeze easily, and are stable. But they don't store as much heat and can be flammable. Inorganic PCMs store more heat but can have other issues like freezing problems or corrosion. Because they store more heat, inorganic PCMs like hydrate salts are good for solar energy storage.
Using Water
Solar thermal plants are often built in deserts because there's a lot of sun. However, some designs need water for cooling, which can be a problem in dry areas. For example, a planned plant in Nevada would need 20% of the water available in the area. Laws in California also prevent using drinking water for cooling.
Other designs use less water. The Ivanpah Solar Power Facility in California saves water by using air-cooling to turn the steam back into water. This reduces water use by 90% compared to traditional cooling, though it might make the plant slightly less efficient. The water is then reused in a closed system, which is good for the environment.
How Efficient is Solar Thermal Energy?
Of all the solar technologies, the solar dish/Stirling engine is the most efficient. A single solar dish-Stirling engine at a lab in the US can produce 25 kW of electricity with an efficiency of 31.25%.
Solar Parabolic trough plants have been built with about 20% efficiency. Fresnel reflectors are slightly less efficient, but they can pack more mirrors into an area, which helps.
The overall efficiency of a solar power plant (considering the total land area) is determined by how much electricity it generates compared to the solar energy that falls on its entire area. For example, the 50 MW AndaSol Power Plant in Spain has an overall efficiency of about 2.6%.
Efficiency doesn't directly mean lower cost. The total cost also includes how much it costs to build and maintain the plant.
Images for kids
-
The 150 MW Andasol solar power station in Spain uses tanks of molten salt to store solar energy so it can make electricity even when the sun isn't shining.
See also
In Spanish: Energía solar térmica para niños