Salami facts for kids
![]() |
|
Type | Sausage |
---|---|
Region or state | Southern, Eastern, and Central Europe |
Main ingredients | Fermented and air-dried pork |
Salami (pronounced sə-LAH-mee) is a special type of sausage. It's made from meat that has been fermented and air-dried. Most often, it's made from pork. Long ago, salami was very popular with people in Southern, Eastern, and Central Europe. This was because it could be kept for a long time without a fridge, even up to 45 days after being cut. This helped people have meat when fresh meat was hard to get. Many countries and regions in Europe have their own special kinds of salami.
Smaller pieces of salami are sometimes called salametti or salamini. Salami is part of a group of cured meats from Southern Europe called salumi. Other salumi include prosciutto and pancetta.
Contents
What Does "Salami" Mean?
The word 'salami' in English comes from the Italian word salame. In Italian, salame is singular, and salami is plural. But in English, we use 'salami' for both one piece or many pieces. Many other languages, like Romanian, Hungarian, and German, use similar words.
The word comes from the Italian word sale, which means "salt." The ending -ame means a group of things. So, salame first meant all kinds of salted meats. Over time, it came to mean the popular kind of salted and spiced meat. This meat is ground up, put into a long, thin casing (like an animal intestine), and then left to dry for weeks or even months.
Where Did Salami Come From?
People have been fermenting food for thousands of years. This process helps good tiny living things grow in food. These good tiny things stop bad or harmful ones from growing. In warm places like the Mediterranean, people dried meat to keep it safe. In colder places, they often smoked it.
The way we make salami today probably started in Italy in the early 1700s. Other countries in Central Europe later started making it too, changing the process a bit. Back then, meat was very expensive, so mostly rich people ate salami.
Today, the main countries that make salami in Europe are France, Germany, Hungary, Italy, and Spain. They make huge amounts of it every year!
Around the world, there are many different kinds of sausages. Each one has its own special spices and flavors. For example, when people moved from Europe to North America, they brought their traditions, like making pepperoni. In the Middle East, people make similar sausages using beef, lamb, or mutton. In China, they have lap cheong, which is usually pork.
In Central Europe, Hungarian salami is very popular. It's often smoked a lot, and then special molds are grown on its surface. In the United States, people celebrate National Salami Day on September 7th each year.
What's in Salami?
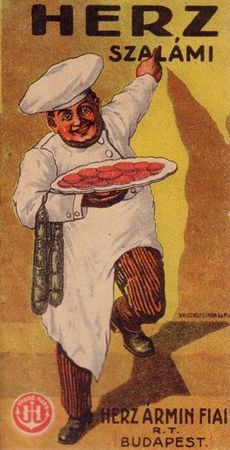
Traditional salami, with its marbled look, is usually made from beef or pork. For religious reasons, halal and kosher salami never have pork. Makers also use other meats like venison (deer meat) and poultry (like turkey). In parts of Northern Italy, goose salami is traditional. Some salami is even made from horse meat or donkey meat, especially in France.
Here are some common extra ingredients in salami:
After mixing the ingredients, makers ferment the raw meat. Then, they stuff it into a casing, which can be natural (like animal intestine) or artificial. The salami is then hung up to cure. Some recipes use a little heat (around 40°C or 104°F) to help the fermentation and drying go faster. Makers often put a special edible mold (like Penicillium) on the casings. This mold adds flavor, helps the salami dry, and keeps it from spoiling.
How Is Salami Made?
Even though salami is not cooked, it's not raw. It's cured. Some types, like Salame cotto from Italy, are cooked or smoked after curing for a special flavor. But they are not cooked for safety reasons.
Making salami involves three main steps: preparing the ingredients, fermentation, and then ripening and drying. Small changes in how the meat is mixed or how it's made create all the different kinds of salami.
Getting Ready
First, the raw meat (usually pork or beef) is ground up. It's often ground coarsely. Then, it's mixed with other things like salt, sugar, spices, and pepper. Sometimes, special bacteria called "starter cultures" are added.
Fermentation Fun
The meat mixture is then put into casings. To get the unique taste and texture of salami, fermentation must happen. This is a slow process where the meat becomes a bit acidic. This acidity helps create the right texture.
For modern salami, makers hang the salami in warm, moist places for 1 to 3 days. This helps the good bacteria grow. Then, they move it to a cool, moist place to dry slowly. In older ways of making salami, they just hung it up right away. Sugars, like dextrose, are added to give the bacteria food.
These bacteria produce lactic acid. This acid lowers the pH of the meat, which makes it harder for bad bacteria to grow. It also gives salami its tangy flavor. The flavor of salami depends a lot on how these bacteria are grown. Long ago, people added wine to help good bacteria grow. Now, they use special starter cultures.
The climate where the salami cures, the size of the casing, and the style of salami all affect how it dries. Scientists have even explored different ways to ferment salami to create various colors and flavors. The most common bacteria used are lactic acid bacteria (LAB) and others like Staphylococcus xylosus. These bacteria help keep the meat safe and last longer. However, makers must choose them carefully, as some can produce things that might be harmful.
Drying Time
After fermentation, the sausage needs to dry. This makes the casings less able to let water through. A white layer of mold or flour on the outside helps protect the meat and fat from going bad.
Drying and ripening happen after fermentation. During this stage, a lot of water leaves the salami. About half of the water evaporates! It's important to prevent too much water loss later by packaging it well. If it dries unevenly, the outside can become hard. In modern factories, the temperature and humidity are carefully controlled based on the salami's size.
Sometimes, nitrates or nitrites are added. These help give the salami its color and stop harmful bacteria from growing. The salt, acidity, and dryness of the salami all work together to make it safe to eat even though it's uncooked. Using fresh, high-quality ingredients is also very important to prevent bad germs from growing.
What Makes Salami Taste So Good?
The quality of salami depends on the ingredients and how it's made. Its smell and taste come from many chemical reactions. The special tangy flavor comes from the bacteria that produce lactic acid. These bacteria also give the meat a nice red color. Other bacteria help create different smells and tastes.
When salami is smoked, it changes the taste, smell, look, and texture. The smoke helps keep the fat from going bad. The smoke also helps create the color of the meat.
Scientists have found over 400 different smells in dry-fermented sausages. For example, Hungarian salami can smell smoky, sweet, spicy, or sour. It might also have hints of cooked meat, cheese, or mushrooms. The smoky smell comes from many different chemicals.
How Long Does Salami Last?
Salami can last a long time because it has very little water and contains things that help preserve it. Salami that's partly ripened will keep its flavor for a while in stores. But eventually, it might start to taste a bit off due to the fat going bad. Harmful bacteria usually don't grow well in dry-cured sausage.
The main reason salami loses its quality is when the fat becomes rancid (goes bad). Other bad flavors like moldy or sour tastes can also appear.
Some studies show that adding coriander oil to salami can help it last longer. It slows down the fat from going bad and keeps the taste and smell fresh. Salami with coriander oil also looks better, with a brighter red color.
Different Kinds of Salami
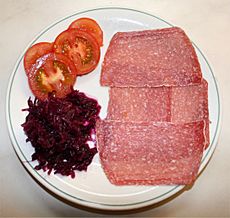
There are many kinds of salami! Here are some from Italy and other places:
- Cacciatore (or "hunter" salami) from Italy
- Ciauscolo, from the Marche region of Italy
- Cotto, a soft, cooked salami that looks like bologna
- Felino, from the Parma area in Italy
- Finocchiona, from southern Tuscany in Italy
- Genovese
- Napoletano, from Naples, Italy
- Milanese, a finely ground salami from Milan, Italy
- 'Nduja
- Soppressata, from Calabria, Apulia, and Basilicata in Italy
- Strolghino
- Ticinese (also called Salame nostrano), from southern Switzerland
Other types of salami include:
- Hard Salami, a smoked salami from Central Europe
- Lovecký salám/Lovecká saláma, a rectangular salami from Czechia and Slovakia
- Pepperoni
- Sibiu Salami from Romania
- Winter salami (Hungarian téliszalámi)
Many old salami types are named after where they come from, like Genoa, Hungarian, and Milano salami. Many have garlic flavor. Some, like certain Hungarian and Italian kinds, use paprika or chili powder. Salami also differs in how finely the meat is chopped and the size of its casing.
Naples-type salami is a popular dry fermented sausage from Southern Italy, made with coarsely chopped pork. In Northeast Italy, traditional dry salami sausages are known for their tangy taste and firm texture. Other popular Italian salamis are made from pork and beef, seasoned with garlic. Pepperoni is often smoked, and chorizo is very spicy and smoked.
Hungarian-type salami is special because it's first lightly smoked, then mold is allowed to grow on it. Szegedi téliszalámi, a Hungarian winter salami, is made from raw pork, bacon, salt, spices, and sugar. It often uses a special pig breed called Mangalitsa and a large casing. It gets a gray mold on its surface and becomes firm after drying for 3 to 4 months.
Dry fermented sausage, or 'salami aeros', is a big product in Greece. Its making often depends on the skill of the maker. These traditional sausages, made without added starter cultures, are often seen as higher quality and are more expensive.
In Germany, Westphalian salami is made quickly from pork, pepper, garlic, and sometimes mustard seeds. It's a smoked, firm salami with a distinct sour taste. The sausages are put into large casings and ripened by slowly lowering the temperature.
In the Netherlands, popular salamis include finely chopped salami, Cervelat, and Boerenmetworst. In Russia, Moscow-type and Russian-type salamis are common, made from pork and beef. Moscow-type salami is known for its large pieces of fat.
Is Salami Healthy?
Some people might be allergic to salami. This can happen because of the special mold used during drying to add flavor. This mold is mostly on the skin of the salami.
The fat used in salami can be high in saturated fat and cholesterol. These are things that doctors say we should watch out for. However, some studies show that makers can replace pork fat with extra virgin olive oil. This changes the fat in salami to healthier types. Salami made with olive oil also becomes more acidic, which is good because it helps stop bad germs from growing.
In 1994, there was a small outbreak of a type of E. coli illness linked to pre-sliced salami from one company. An investigation found that the factory followed all rules, and there was no sign of contamination after the salami was made. This shows how important it is for food companies to be very careful with food safety.
Keeping meat products safe is very important. Some fungi can make meat look and taste bad, and some can even produce harmful toxins. But some fungi, like those on the surface of dried salami, are harmless and show that the salami is aging well. So, makers must remove any fungi that could be bad for people.
Scientists are also looking into using natural things, like coriander, oregano, and clove oils, as preservatives in salami. These oils can help stop harmful fungi from growing. Researchers test how much oil to use so it works as a preservative but doesn't change the salami's flavor or look too much.
See also
In Spanish: Salami para niños
- List of dried foods
- List of sausages
- List of smoked foods
- Salchichón and Chorizo – two similar types of pork sausages from Spain and Portugal
- Saucisson – a similar type of pork sausage from France
- Summer sausage