Oliver Evans facts for kids
Quick facts for kids
Oliver Evans
|
|
---|---|
![]() "Oliver Evans, the Watt of America"
Original portrait caption |
|
Born | |
Died | April 15, 1819 New York City, New York, USA
|
(aged 63)
Nationality | American |
Occupation | Inventor, engineer |
Spouse(s) |
Sarah Tomlinson
(m. 1783–1816)Hetty Ward
(m. 1818–1819) |
Children | Three sons and four daughters |
Signature | |
![]() |
Oliver Evans (born September 13, 1755 – died April 15, 1819) was an amazing American inventor and engineer. He was born in the countryside of Delaware and later worked in Philadelphia. Oliver Evans was one of the first Americans to build steam engines. He was also a big supporter of using high-pressure steam, which was a new idea at the time.
Evans was a leader in automation, moving materials, and steam power. He was one of the most important inventors in the early days of the United States. He created many things. His most famous inventions include the first fully automated factory process, the first high-pressure steam engine, and the first amphibious vehicle (a vehicle that can travel on both land and water). He also made the first American automobile.
Born in Newport, Delaware, Oliver Evans didn't have much formal schooling. When he was a teenager, he became an apprentice to a wheelwright, someone who builds and repairs wheels. Later, he worked with his brothers to design and build an automated mill. This mill used devices like bucket chains and conveyor belts. It was a continuous process that didn't need people to move things around. This idea was very important for the Industrial Revolution and mass production.
Later in his life, Evans focused on steam power. In 1801, he built the first high-pressure steam engine in the United States. He developed his design on his own, just a year after Richard Trevithick built the first one in the world. Evans really pushed for high-pressure steam engines to be used in America. He also dreamed of building a steam car. In 1805, he built and ran one called the Oruktor Amphibolos. It was the first automobile in the country and the world's first amphibious vehicle. However, it was too simple to be truly successful.
Oliver Evans was a visionary. Many of his ideas were far ahead of their time. For example, in 1805, he was the first to describe how vapor-compression refrigeration works and designed the first refrigerator. But it took 30 years for his friend Jacob Perkins to build a working one. He also drew plans for a solar boiler, a machine gun, a steam-carriage gearshift, and many other things that weren't built until after he died. Evans had powerful friends, but he wasn't very good at getting along with people. He often felt that his work wasn't recognized. This made him angry and bitter later in life, which hurt his reputation. Even though his work was very important, he isn't as famous as other steam pioneers of his time.
Contents
Early Life and First Inventions (1755–1783)
Oliver Evans was born on September 13, 1755, in Newport, Delaware. His father, Charles Evans, was a shoemaker. The family moved to a farm when Oliver was very young. Oliver was one of 12 children. We don't know much about his early life or schooling. But he was a strong reader and writer from a young age.
When he was 17, Oliver became an apprentice to a wheelwright in Newport. His master was very strict and wouldn't let him use candles to read at night. So, Oliver collected wood scraps from his work to make small fires for light. The American Revolutionary War started when Evans was 19. He joined a local militia but didn't fight in any battles.
By age 22, Evans started making fine wire for carding machines. These machines were used to comb fibers for making thread. He wanted to make this process faster. So, he invented a machine that could bend and cut wire quickly. This helped make the parts for textile cards. George Latimer, a local judge, saw how useful it was. He had a blacksmith build the machine, and it was a success in 1778.
Evans wanted to do even more. He developed a machine to punch holes in the leather where the wire teeth were inserted. This invention made card manufacturing much faster, producing about 1,500 teeth every minute! However, Evans couldn't find money to sell his invention. Still, his ideas inspired others. Over the next 20 years, automated textile card production grew a lot, especially with the rise of the cotton industry in the South.
During this time, Evans also started experimenting with steam power. In 1783, he applied for a patent in Delaware for a steam-powered wagon. But his request was denied because he hadn't built a working model yet. That same year, at age 27, Evans married Sarah Tomlinson.
Building the Automated Flour Mill (1783–1790)
In the early 1780s, Evans became interested in flour milling. This industry was growing fast in northern Delaware. Back then, operating a grist mill took a lot of hard work. Workers had to manually move grain from one step to the next: grinding, cooling, sifting, and packing. Some steps, like cooling, were very slow.
Also, the quality of flour in colonial America was often poor. Mills didn't grind hard wheat well enough, leaving coarse, brown flour. Dirt and other impurities often got into the flour because so many people were moving around the mill. Evans realized that the process needed too many workers and produced low-quality flour.
In 1783, two of Evans's brothers started building a mill in Newport. Evans helped design it. When the mill opened in 1785, it was a regular mill. But over the next five years, Evans started inventing machines to reduce the need for workers.
Moving wheat from the bottom to the top of the mill was the hardest job. Evans's first invention was a bucket elevator. This machine used chains of buckets to lift grain and flour from one process to the next. Bucket chains had been used since ancient Roman times for lifting water. Evans saw diagrams of them for ships and realized they could be used for grain.
Another tough job was spreading out the warm, moist flour after grinding so it could cool and dry. Workers usually shoveled it by hand across large floors. Evans invented the "hopper boy." This device collected flour from the bucket elevator and spread it evenly over the drying floor. A mechanical rake would spin around, leveling the flour and slowly moving it towards central chutes for sifting. These two inventions saved many hours of labor and kept the flour cleaner.
These machines weren't revolutionary on their own. But Evans's overall idea was! He wanted to change how manufacturing worked. He saw it as one continuous, connected process, not just separate steps. This meant a factory could be fully automated. The key was moving materials smoothly without human help. This was the first fully automated industrial process. The idea of continuous production became super important for the Industrial Revolution and later for modern mass production.
Building these complex machines was hard. Evans struggled to find money to pay skilled carpenters. The big flour milling industry nearby, on the Brandywine River, was run by Quaker millers. They didn't see much value in Evans's ideas. One merchant even told him, "Oliver, you cannot make water run uphill, you cannot make wooden millers!"
But George Latimer, the son of that merchant, believed in Evans. He helped Evans get patents for his inventions in 1787 and 1788. By this time, Evans had turned his brothers' mill into a fully automated test model. The Evans brothers offered free licenses for their designs to the first miller in each county who would hire Evans to update their mills. But this plan didn't work well, and few people were interested.
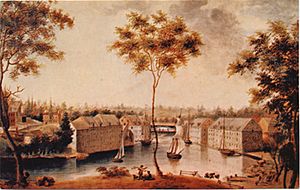
Evans was not very patient and got frustrated easily when people didn't understand his ideas. His inventions were often too advanced for his time. The idea of a fully automated factory was hard for people to grasp. Evans once recalled how some millers visited his automated mill. He purposely stayed hidden so they could see it running without anyone there. He then explained how it worked, thinking they would be impressed. But they went back to Wilmington and called his mill "a set of rattletraps."
After years of trying, Evans's designs finally got a chance on a larger scale. In 1789, the Ellicotts, a Quaker family in Baltimore, invited Evans to update their mills. The updates were a success! Evans worked with Jonathan Ellicott to create a modified Archimedean screw that could move materials horizontally, working with his vertical bucket elevators. He added other machines, and now he had a full set of material-handling machines.
In 1790, Evans moved to Wilmington and built a working model of his designs. His inventions got a big boost when a leading miller, Joseph Tatnall, converted his mills to the Evans system. Tatnall estimated that the changes saved him $37,000 in one year! Other local millers quickly followed. Soon, Brandywine Village became a showcase for Evans's milling technology. Finally, the Brandywine millers were convinced. Automated mills quickly spread across the eastern United States.
In 1790, when the first federal patent law was introduced, Evans immediately applied for protection for his milling designs. He was granted the third U.S. patent ever! His application was personally reviewed and approved by important figures like Secretary of State Thomas Jefferson, Secretary of War Henry Knox, and Attorney-General Edmund Randolph.
Writer and Merchant (1790–1801)
After getting his patents and seeing his designs adopted, Evans looked beyond Delaware. His brother Joseph traveled widely to promote Evans's work. By 1792, over 100 mills were using Evans's machines. When George Washington visited Joseph Tatnall in 1790, he saw Evans's technology at work. Washington was so impressed that he had his own gristmill at Mount Vernon converted to the Evans system in 1791. Evans's brothers oversaw this work.
In 1793, Evans sold his share in the Red Clay Creek mill. He moved his family from Wilmington to Philadelphia, where he opened a store selling milling supplies.
His first years in Philadelphia were mostly spent writing. Evans initially planned a small guide for millers. But he got so involved that he spent several years writing a huge book on milling technology. It included long chapters on physics, hydraulics, and mechanics. Sometimes, he even neglected his family's money to finish it.
His book, The Young Mill-wright and Miller's Guide, was published in 1795. It had five parts: 'Principles of Mechanics and Hydraulics', 'Of the different Kinds of Mills', 'Description of the Author's Improvements', 'On the Manufacturing of Grain into Flour', and 'Ellicott's Plans for Building Mills'. It also had an appendix with ideas for other inventions, like a hot-air central heating system. Thomas Ellicott, whose family used Evans's designs in Baltimore, wrote a section on mill construction.
Much of the book's theory came from earlier scientific work. But Evans made sure the theories matched his own experiments and observations. For example, he found that what was written about waterwheels didn't match what he saw in practice. So, he updated the theories based on his observations. He said, "neither the old or new theories agree with practice, therefore we must suspect that they are founded on error."
The first edition of the guide, published in 1795, had famous subscribers like George Washington and Thomas Jefferson. The book became very popular. It was a key manual for millers for over 50 years, with 15 editions printed between 1795 and 1860. Its popularity came from its detailed, practical explanations of mill design. It was the main guide for American milling until after the American Civil War.
After the book was published, Evans focused on his store and earning money from licensing his patented designs. More millers started using his machines after 1800, and his wealth from license fees grew quickly. He expanded his store in Philadelphia, became an agent for English imports, and hired blacksmiths for complex metal work. Evans also kept improving mill designs. He patented a new way to make millstones and developed a screw mill for grinding plaster of Paris.
Inventing the High-Pressure Steam Engine (1801–1806)
Steam engines started appearing in the United States in the late 1700s. Evans saw early examples in Delaware and Philadelphia. John Fitch launched a simple steamboat on the Delaware River in the late 1780s. By 1802, the Philadelphia waterworks used two low-pressure steam engines to pump water. But most steam engines were in Europe, developed by inventors like Thomas Newcomen and James Watt.
Evans first thought about using steam for transportation in the 1780s. He designed basic 'steam carriages' in the 1790s. In 1801, he seriously started working on his dream of a steam carriage. Other engineers, like William Murdoch, had also tried to build steam-powered carriages. But they found that low-pressure, spinning steam engines weren't powerful enough to move a heavy carriage.
So, Evans focused on a reciprocating engine, which uses a piston moving back and forth. He became an early supporter of 'strong steam' or high-pressure engines, like Richard Trevithick. Watt and other early steam pioneers avoided high-pressure steam because the metal technology wasn't advanced enough. Evans realized that a high-pressure steam engine could be much smaller but still provide the same or more power than low-pressure ones. This was key for a steam carriage.
Some high-pressure steam engine experiments had been done in Europe, like Trevithick's Puffing Devil in 1801. Trevithick avoided Watt's patent by simply removing the condenser. People feared that high-pressure steam boilers would explode. Watt even wanted Trevithick jailed for the danger his engines posed. But Evans ignored these fears. He developed his own high-pressure engine designs without Watt's condenser. His designs included a grasshopper beam, a double-acting cylinder, and four steam valves, similar to Trevithick's. Each valve was controlled by its own cam.
The result was a high-pressure steam engine that had more power for its weight than Newcomen engines. This made it useful for locomotives and steamboats. These engines were also simpler than condensing engines, making them cheaper to build and maintain. They didn't need large amounts of water for condensing. These features made them good for many industrial uses.
Just like with his automated mill, other engineers criticized Evans's ideas. Benjamin Latrobe, an influential engineer in Philadelphia, was a notable critic. It's believed that Evans didn't know about Trevithick's similar work in Europe.
Building his designs was much harder than Evans expected. In the U.S. at that time, there were only six working steam engines and few workshops that could make them. It took Evans much of his savings and two years to build a working model. He displayed it to the public in 1803. This first engine had a double-acting cylinder six inches wide and an eighteen-inch piston stroke. Many parts, like the flywheel and crosshead, were made of wood to make it easier to build. The boiler, which was crucial for safety, was a large copper shell covered in wood and cast iron rings to hold the pressure. The machine produced about five horsepower. This was modest compared to the nearby waterworks engine, which produced 12 horsepower. But Evans's engine was tiny—about 25 times smaller in volume than the waterworks machine.
Evans showed his engine at his store. He used it to crush plaster of Paris and, more excitingly, to saw large slabs of marble. This showmanship worked! Thousands came to see the machine. The Philadelphia newspaper Aurora announced "a new era in the history of the steam engine."
The Oruktor Amphibolos
Evans received a patent for his new steam engine in 1804. He started looking for ways to use it commercially. His first idea was for the Lancaster Turnpike Company. He suggested building a steam wagon that could carry 100 barrels of flour between Philadelphia and Lancaster in two days. He thought this would be more profitable than using five horse wagons, which took three days. Evans boldly stated, "I have no doubt but that my engines will propel boats against the current of the Mississippi, and waggons [sic] on turnpike roads with great profit." But the company wasn't sure about the new technology and rejected his idea.
Despite this, Evans found a client within a year. The Philadelphia Board of Health needed to dredge and clean the city's dockyards. In 1805, Evans convinced them to hire him to build a steam-powered dredge. The result was the Oruktor Amphibolos, which means "Amphibious Digger."
This vehicle was a flat-bottomed scow with bucket chains to scoop up mud and hooks to clear obstacles. A high-pressure Evans engine powered both the dredging equipment and the movement of the vehicle. It was nearly 30 feet long, 12 feet wide, and weighed about 17 tons. To move this huge machine to the waterfront, and to show off his idea of land-based steam transportation, Evans put the hull on four wheels. He connected the engine to the wheels. On July 13, 1805, the Oruktor drove from his workshop through the streets of Philadelphia to the Schuylkill River.
The Oruktor Amphibolos is believed to be the first automobile in the United States. It was also the world's first motorized amphibious vehicle. However, there are few reliable accounts of how well it worked. Evans often exaggerated its success. He claimed it drove successfully around Philadelphia and even circled his rival Benjamin Latrobe's waterworks before launching into the river. But its great weight and limited engine power make it unlikely it traveled far on land. We also don't know how well it worked as a steamboat. It proved ineffective as a dredger and was scrapped for parts in 1808.
Still, Evans's dream of steam carriages was not impossible. In 1812, he wrote a futuristic description of a world connected by shipping lines, railroad tracks, and steam locomotives. He accurately described what would happen in the future. The Italian model company, Brumm, made a 1/43 scale model of this steam carriage. It's a rare model of an early steam vehicle.
The Steam Engineer's Guide
Evans often argued with other inventors and engineers about steam technology. His frustration led him to publish a book earlier than he planned. He hoped it would be as successful as his milling guide. The Steam Engineer's Guide was shorter and less organized than his first book. One-third of the book was an argument between Evans and John Stevens, another famous steam engineer. Evans added more criticisms of Stevens's ideas.
Evans ended his book by saying he would stop inventing because he felt unappreciated and that it wasn't profitable. But he would make similar statements many times later. Still, the Steam Engineer's Guide became popular, though not as much as his milling guide. It was the first book in the U.S. to make steam engineering ideas accessible to everyone.
The book starts with an introduction to steam engine principles and relevant physics. It also includes designs for Evans's high-pressure steam engine, boilers, and screw-mills. Evans created tools and tables for steam engineers, just like he did for millers. These included tables showing heat and pressure limits of metals, instructions for building steam systems, and diagrams for parts like valves and boilers.
Evans also used the book to say that high-pressure steam engines were safe if built correctly. This was despite the fact that he himself had experienced several boiler explosions in his workshop. At that time, thermodynamics (the study of heat and energy) was not well understood. So, many of Evans's theories, including his "grand principle" for steam engines, had flaws. Even though Evans was very successful in developing high-pressure steam engines, his theoretical understanding was limited. He often couldn't accurately predict how much power his machines would produce or how much fuel they would need.
The guide also covered many other topics Evans was interested in. It included a collection of inventions by others that he thought were important, like a straw-cutter and flour press by his brother Evan.
Evans suggested that engineers needed better scientific data. He tried to create 'The Experiment Company', a private research group to conduct experiments and gather data for its members. But it failed because he couldn't find investors, possibly because he wanted the company to develop his own steam wagon. The Franklin Institute, founded in Philadelphia a few years after Evans's death, was based on similar ideas.
Refrigeration Ideas
Even with an incomplete understanding of science, Evans's ideas for steam engines were ahead of his time. In his Steam Engineer's Guide, Evans noted that creating a vacuum over water makes it boil at a lower temperature and cools it. He also observed that a vacuum would have the same effect on ether, and this cooling should be enough to make ice.
He then described a piston vacuum pump that could do this. He also showed that a compression cylinder would produce heat in a condenser. So, Evans created the first detailed and scientifically sound design for a vapor-compression refrigerator. He identified all the main parts: expander, cooling coil, compressor, and condenser. Some people call him the 'grandfather of refrigeration' because of this.
Evans never built a working model of his refrigerator. But later in life, he worked with inventor Jacob Perkins on steam engines and refrigeration. Perkins later built a refrigeration device based on many of Evans's original ideas, getting patents for it in 1834–1835.
Mars Works and New Engines (1806–1812)
After perfecting his steam engine ideas, Evans focused on selling his inventions. His first steam engines were built without special tools or experienced workers. He relied on blacksmiths. But Evans soon realized that, unlike his wooden milling machines, he needed special skills, precise tools, and a large foundry to build steam engines commercially.
So, Evans built the Mars Works in Philadelphia. He named it after Mars, the Roman god of war. This was a challenge to the famous Soho Foundry in England, which built Watt and Boulton engines. The Mars Works became one of the largest and best-equipped factories of its kind in the U.S. It had a large foundry, a moldmaker's shop, blacksmith shops, a millstone maker, and its own steam engine to grind materials. With over 35 staff, the Mars Works made many products, from steam engines to cast iron parts, and milling and farming machines.
Steam engine orders alone weren't enough to cover the high costs. So, the works became skilled at producing all kinds of heavy machinery. This helped Philadelphia become a major center for such work in the 1800s. The Mars Works even received military orders, casting naval cannons during the War of 1812. Evans was also very innovative in designing steam power solutions. For example, when commissioned to build engines for wool factories in Middletown, Connecticut, he designed a system of pipes and radiators to heat the factory using engine exhaust.
We don't have records of the early steam engines made by the Mars Works. But Evans's most famous engine design appeared around 1812. He called it the Columbian Engine as a patriotic gesture. It was his most advanced and successful steam engine. This horizontally designed engine allowed the crankshaft and piston rod to work closely together at one end. This reduced the need for a heavy working beam, common in other engines. The piston rod was kept in a straight line by a new type of linkage. This linkage is still known as the Evans straight-line linkage.
The Columbian was the best example of the grasshopper-style steam engine. Its perfected design made this style popular for many uses. In 1813, Evans added a condenser to the Columbian design. This greatly reduced the engine's running cost. At this point, his engines were as efficient and powerful as low-pressure Watt-Boulton designs, but much cheaper to build and smaller. Within a year, 27 Columbian engines were working or being built for uses like sawmilling, grain milling, and making paper, wire, and wool.
Pittsburgh Steam Engine Company
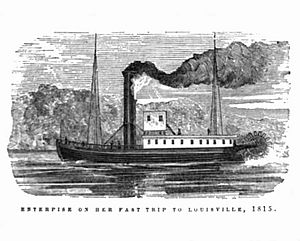
As the Mars Works' reputation grew, so did the demand for its products. After a few years, the Mars Works started exporting engines inland. Oliver Evans's son George moved to Pittsburgh in 1809 to run the Pittsburgh Steam Flour Mill. George and the mill were very successful, creating a lot of interest in Evans's engines in the western parts of the country.
However, shipping engines to western Pennsylvania, Kentucky, or Ohio was difficult and expensive. In 1811, Evans, George, and another successful steam miller, Luther Stephens, founded the Pittsburgh Steam Engine Company. Like the Mars Works, this company would produce heavy machinery and castings in Pittsburgh, Pennsylvania. With high demand and little industrial capacity, the Pittsburgh works also started making brass items and finer products like hinges.
The Pittsburgh factory's location near the Mississippi River was important for developing high-pressure steam engines for steamboats. The new company began promoting its engines for river transport. Evans had long believed in using steam engines for boats.
Evans knew John Fitch, who built the first steamboat in the U.S. They had worked together. The Oruktor Amphibolos was Evans's only attempt at building his own high-pressure steamboat. Evans himself was often vague about its abilities. But Robert Fulton found success with the North River Steamboat on the Hudson River in 1807, making steamboats a reality. Fulton used low-pressure engines, but in 1812, he contacted Evans about using Evans's engines. However, this didn't lead to Evans's designs being used on Fulton's ships.
The Mississippi and its tributaries had much stronger currents than eastern rivers. Low-pressure steamboats weren't powerful enough to go against them. The Enterprise was the first successful steamboat on these rivers. Its designer, Daniel French, used an adapted Evans engine. High-pressure engines became the standard on the Mississippi. However, few were actually built by the Pittsburgh works because Evans's patent on high-pressure engines wasn't widely enforced. Many other engine shops opened on the Mississippi and freely copied Evans's designs.
Some notable river steamboats built by the Pittsburgh and Mars Works included the Franklin, the Aetna, and the Pennsylvania. Another boat, named the Oliver Evans but renamed the Constitution, sank near Point Coupee, Louisiana, after its boiler exploded. Eleven crew members died. Evans was very upset by the news. He defended the safety of high-pressure engines, saying explosions were very rare.
Patent Challenges
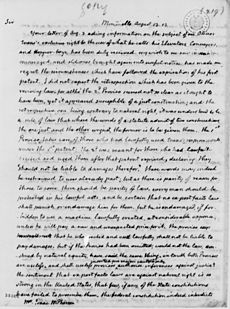
Evans often had to fight to protect his inventions. He was most persistent in his later years, especially with his successful flour-milling patents. His original patent for his automated flour mill expired in January 1805. But Evans thought the 14-year patent term was too short. He asked the Congress to extend it.
In January 1808, "An Act for the Relief of Oliver Evans" was passed and signed by President Jefferson, who admired Evans. This act took the unusual step of bringing Evans's expired patent back to life and giving him another 14-year term. Evans was thrilled. But this caused problems, especially for millers who had started using Evans's designs between 1805 and 1808, after the patent first expired. Many millers had waited for the patent to run out before upgrading their mills.
Evans and his agents aggressively collected royalties from those using his designs. He also greatly increased the license fees, leading to accusations of extortion. Many cases ended up in court. The 1808 act protected those who adopted Evans's technology from 1805 to 1808. But it didn't clearly state if this protection was forever (as defendants argued) or only for those three years (as Evans argued).
By this time, Evans had a poor reputation among millers. His harsh and often petty pursuit of patent rights made people resist him more. Several major legal cases questioned if laws extending private patents were even constitutional. But Evans usually won these cases.
The most bitter legal battle started in 1809. Evans sued Samuel Robinson, a miller near Baltimore, who was using Evans's improvements without a license to produce a small amount of flour. Evans asked for $2,500 in damages. Many thought this amount was unfairly high. Evans's actions united the Baltimore community against him. When the case was finally heard in 1812, many people supported Robinson.
Evans's critics presented evidence that Evans didn't truly invent much of what his patents protected. While the hopper-boy was original, bucket chains and Archimedean screws had been used since ancient times. Evans had only modified them for milling. A retired Thomas Jefferson wrote letters to both Evans and his critics. He questioned what "invention" and "machine" truly meant. But he ultimately defended patent law, saying it encouraged innovation by rewarding inventors. Jefferson noted that even though Evans's designs used old devices, only Evans had thought to combine and modify them to build an automatic mill.
The jury found in favor of Evans, but it was a difficult victory. Evans had angered most of the milling community. He eventually reduced his claim against Robinson to $1,000. In response, a prominent critic, Isaac McPherson, asked Congress to limit the money Evans could seek or to cancel his patent entirely. The Senate drafted a bill to reduce some of Evans's patent rights, but it didn't pass. Evans continued to aggressively pursue his patent fees. Many of these issues, including what counted as originality in a patent, were finally addressed in the Patent Act of 1836.
Later Life and Passing (1812–1819)
Oliver Evans often suffered from sadness and bitterness. He felt that people didn't appreciate his inventions. These feelings seemed to get worse in his later years. During one of his many legal battles in 1809, a judge's comments made Evans so angry that he dramatically burned many of his invention plans and papers. He said that inventing had only brought him heartache and disappointment. He vowed to focus only on business and making money for his family. Luckily, what he burned was only a small part of his work. He did continue inventing, but his later life was marked by hostility and disappointment.
Evans slowly stepped back from running his workshops. His son George managed operations in Pittsburgh. His sons-in-law, James Rush and John Muhlenberg, managed the Mars Works in Philadelphia. By now, the Mars Works was well-known. It received important orders, like the engines for the Philadelphia Mint in 1816. Records show that the Mars Works built over 100 steam engines by the time Evans died.
In retirement, Evans became very focused on collecting patent fees from those using his technology, which was now widespread. In 1817, he said his time was "wholly engrossed by law suits." Evans became almost obsessed. He wrote to his many lawyers (he had 15 working on his cases across the U.S. at one point) his final work. It was called Oliver Evans to His Counsel: Who are Engaged in Defence of His Patent Rights, for the Improvements He Has Invented. Evans even traveled to distant parts of the country to find people violating his patents. On a trip to Vermont, he visited mills and then hired a lawyer to sue 22 of them!
In his last years, Evans made a list of all his inventions—80 in total. This list is now lost. Some of his unfinished ideas included a plan for gas lighting in cities, a way to raise sunken ships, a machine gun, a self-oiling shaft bearing, different types of gearshifts for steam carriages, a dough-kneading machine, and a perpetual baking oven. In 1814, during the War of 1812, when the British Navy threatened Washington, D.C., Evans offered to build a steam-powered frigate, but the idea didn't go far.
In 1816, his wife Sarah died. Two years later, in April 1818, Evans married Hetty Ward, who was much younger than him. She was the daughter of a New York innkeeper. In his last years, Evans lived in New York with his new wife. In early 1819, Evans got a lung inflammation. After a month of illness, he died on April 15, 1819. Just four days before, he heard that the Mars Works in Philadelphia had burned down. However, his sons-in-law were determined to rebuild the business, which they did outside the city.
Evans was buried at Zion Episcopal Church in Manhattan. But when that church was sold, his body was moved several times. Finally, in 1890, he was laid to rest in an unmarked common grave at Trinity Cemetery, Broadway at 157th Street, New York City.
Oliver Evans's Lasting Impact
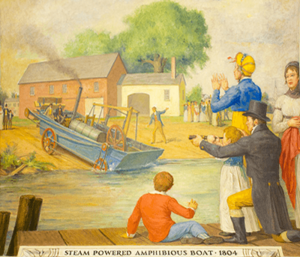
Oliver Evans's contributions to milling were truly important and quickly adopted. During his lifetime, American milling changed completely. His designs allowed mills to be built on a large, industrial scale, making them much more efficient. This made milling more profitable, and the number of mills in the U.S. grew dramatically. The price of flour dropped a lot, and its quality improved. This led to a big change in bread making. Cheaper, better flour meant bread was cheaper to make. Within a generation, most people bought bread from stores instead of making it at home.
The impact was even bigger in Europe. The "American System" was quickly adopted by the milling industry there. This led to huge increases in food production, which was much needed during the Napoleonic Wars around 1800.
While Evans only modified some parts of his designs, like bucket elevators and Archimedean screws, his idea of combining many machines into an automated, continuous production line was unique. This idea was crucial for both the Industrial Revolution and the development of mass production. Today, historians often credit Evans as the first in a line of industrialists that led to Henry Ford and the modern assembly line. His concept of industrial automation was far ahead of its time. It took more than a century for this idea to be fully realized in manufacturing. However, continuous process manufacturing spread from Evans's milling designs to other industries like brewing and baking, and eventually to many other products. The famous industrial historian Sigfried Giedion said that Evans "opens a new chapter in the history of mankind" because of this.
Restored Evans Mills |
---|
Colvin Run Mill in Fairfax County, VA |
Keefe-Mumbower Mill in Montgomery County, PA |
Newlin Mill in Delaware County, PA |
Peirce Mill in Washington, D.C. |
Sugar Loaf Mill in Augusta County, VA |
Washington's Gristmill in Fairfax County, VA |
Yates Mill in Wake County, NC |
Evans's work with steam engines wasn't as groundbreaking as his milling inventions. But he played a key role by inventing and spreading the high-pressure steam engine in the United States. Evans's engines, especially the Columbian, were very important for early steam power in the U.S., particularly for steamboats and industrial processes. Yet, again, Evans was ahead of his time. He died when steam power was still new in the U.S., so many of his ideas took time to become common. For example, even though he was a big supporter of high-pressure engines, they didn't fully replace low-pressure designs until the 1830s. And his dream of a steam wagon, despite the brave attempt of the Oruktor Amphibolos, didn't become widespread until much later. Unlike his earlier contributions, Evans was just one of many brilliant minds working on steam technology. Another inventor, Richard Trevithick, working completely separately from Evans, also developed the high-pressure engine that made steam travel possible.
Despite his amazing inventions and importance in technology, Evans never became a household name. In some ways, Evans was his own worst enemy. He was deeply affected by feeling that his work wasn't recognized. His sadness sometimes made him act in extreme ways, like ending projects early and vowing to stop inventing many times. Over time, these feelings turned into bitterness and anger towards those who criticized him. He became known for being loud and argumentative, often exaggerating his achievements and fiercely attacking critics (like his wild claims about the Oruktor Amphibolos later in life). While his constant pursuit of patent rights did make people pay him, it badly hurt his reputation and made him many enemies. A leading Philadelphia merchant summed it up in 1802, saying "few if any [millers] are inclined to give pompous blockhead, Oliver Evans, the credit of inventing any of the useful contrivances in milling for which he now enjoys patents."
Yet, despite his struggles and critics, Evans was incredibly persistent in pursuing his ideas. He believed this quality would ultimately lead him to triumph. The French translator of the Young Steam Engineer's Guide agreed, writing that "posterity will place his name among those who are most truly distinguished for their eminent services rendered to their country and to humanity."
Images for kids
-
Thomas Jefferson's letter to Isaac McPherson in 1813